summary
In today's increasingly competitive global marketplace, efficient industrial production typically depends on the speed, accuracy and reliability of each factory automation system. Even in areas with low labor costs, manufacturers are eager to improve the precision of their automation systems because they know that if they don't, they will endanger their position in the global economy.
At the heart of industrial automation is a new generation of advanced smart sensors that keep production lines running, connected to high-performance programmable logic controllers (PLCs) and human machine interface (HMI) systems through low latency and real-time networks. Of course, time is money for manufacturers. Efficient production lines will continue to operate as quickly as possible as long as the manufactured products are able to reach the required level of quality. High-speed, reliable sensors must monitor or measure various states of the production line very quickly (in milliseconds or even faster). The network must then transmit this information with minimal time delay and without disrupting production. We need a large number of industrial communication protocols to achieve the required key communication performance, such as: PROFIBUS?/PROFINET?, Ethernet/IPTM, EtherCAT?, POWERLINK, SERCOS? III, etc. In addition, processing components such as PLCs must respond correctly in real time, otherwise productivity will be affected and loss of profits (see Figure 1 below).
Texas Instruments (TI) has extensive experience in providing comprehensive, high-performance, efficient, and scalable technologies for industrial automation. Texas Instruments' extensive line of analog and embedded processor products enables customers to design complete system-level solutions. This article highlights TI's innovative, highly differentiated solutions that make industrial communications less costly, easier to access, and drive automation and productivity gains.
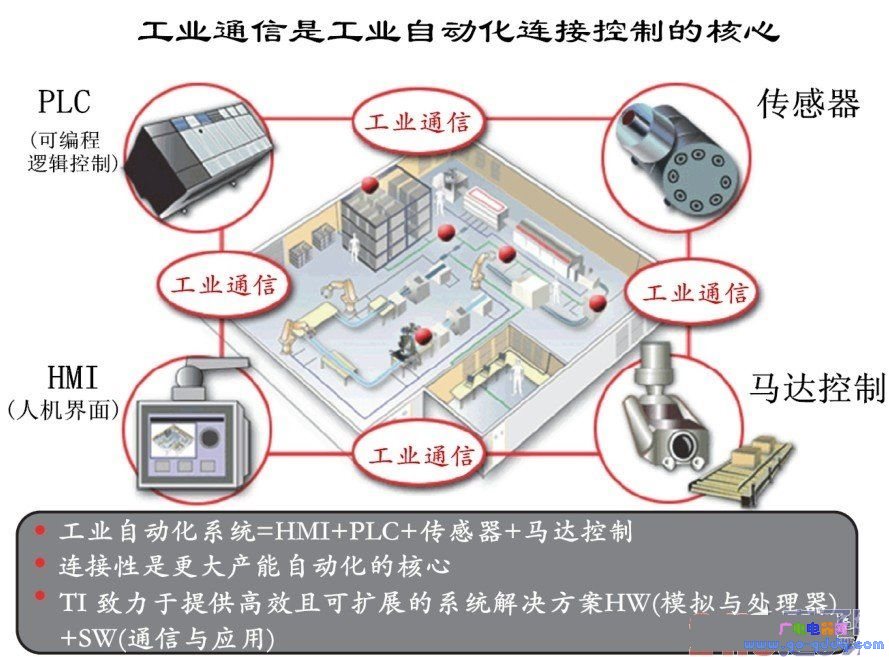
Figure 1 HMI + PLC + sensor + motor controlled industrial automation system
Industrial Automation Introduction
A typical industrial automation system typically consists of four major components, between which low latency and real-time high-speed communication can be implemented. The four components are: sensor, human machine interface, PLC and motor driver.
sensor
The information and data transmission of modern factory automation systems is increasingly dependent on smart sensors. In the past, sensors were only responsible for monitoring and measuring, but not for analysis. Now, as sensors become smarter, they are better able to evaluate the work they are testing and get the job done in real time. Many of the sensor's functions include temperature, motion, optical object and position, weight, acceleration, chemical composition, gas, air pressure or other pressure, liquid flow, and other aspects of the physical world.
Human Machine Interface (HMI)
A human machine interface is a unit or subsystem that communicates with a controller. Using state-of-the-art technology, the human-machine interface of most industrial automation systems integrates graphical display subsystems such as touch screens, which are intuitive and easy to learn.
Programmable Logic Controller (PLC)
In general, PLCs are microcontroller- or processor-based systems that receive information from a variety of sensors and system operators distributed throughout the plant. Based on the information provided by the two sources, the PLC initiates actions to control the production line.
Motor driver
The motor drive is some machine part that actually responds to PLC commands. For example, in a car assembly plant, the sensor provides the PLC with information about the position of the car body. The PLC responds to this information by issuing an instruction to the motor control unit to control the robot arm to spot weld the car.
In industrial automation systems, these four major connections are achieved through high-speed, low-latency networks. This network ensures a fast response to the PLC's sensor or operator information input. In general, today's industrial automation systems are real-time, decision-making, high-precision systems that precisely control high-speed production processes.
Future challenges
The basic challenges that industrial automation will face are the same as the challenges we have overcome. To achieve better results, control systems must continue to improve their real-time responsiveness, reliability, accuracy, precision, and overall maturity. An essential condition for meeting these requirements is the continuous development of networking and other networking technologies.
In the industrial automation market, there are more than 120 serial communication standards and 25 Ethernet-based protocols, all of which can be deployed in our factories today. The problem is that what we lack is not the solution, but their diversity and the way they are deployed.
Every popular industrial communication protocol, such as PROFIBUS/PROFINET, EtherCAT, Ethernet/IP, etc., has one or more important sensors, PLC, HMI and motor driver suppliers behind the scenes. Implementing industrial automation systems using components from multiple vendors typically requires the deployment of several communication protocols supported by multiple vendors. This increases the complexity of the overall system and increases costs. For example, many automation systems today typically use a central processing unit (CPU) to run applications and then use another discrete component such as an application specific integrated circuit (ASIC) or field programmable gate array (FPGA). ), specifically for communication protocol processing. This is especially true in some automation components that are considered as slave devices by communication protocols.
Most industrial automation communication protocols use a hierarchical master/slave architecture. The main device is generally a PLC, or some intelligent control unit. The slave device is typically a motor driver and some sensors that do not initiate an action or control process. In order to achieve the high speed, low latency communication required by the automation system to carry the network, many protocols enhance the media access (MAC) layer functionality associated with these slave devices. This imposes a greater burden of local protocol processing on the slave device, ultimately resulting in the use of protocol processing dedicated ASICs or FPGAs in distributed slave devices. And because the slave devices in industrial automation systems are usually more than the master devices, the overall system cost is greatly increased.
TI is working with you to meet the challenge
Meeting these challenges in industrial automation requires advanced technology to enable communication networking and rationalization. TI is committed to providing industrial automation system manufacturers with complete solutions for embedded processors, sensors, software building blocks and supporting tools. This technology must be simple and cost-effective to meet the requirements of critical components (PLCs, HMIs, sensors, and motor drives) in such systems, while supporting the grading requirements of master and slave devices. In addition, TI focuses on providing an efficient support solution that simplifies the deployment of its factory automation systems to meet the diverse needs of its customers.
The success of TI solutions is demonstrated by the excellent performance of SitaraTM ARMTM-based processors in industrial automation applications. Sitara AM18x ARM9TM (and the latest AM335x ARM CortexTM-A8 System-on-Chip (SoC)), integrates multiple processing cores, real-time communication accelerators for multi-protocol processing, real-time and advanced operating systems, graphics processing and numerous other resources The processing work to overcome the challenges of industrial automation in the coming years.
In particular, the AM335x ARM Cortex-A8 SoC is an example of TI's industrial automation development strategy. Using processing speeds from 275 GHz to 1 GHz, the AM335x SoC can handle the processing requirements of smart sensors to PLCs and other automation components in between. In addition, the low power consumption allows the AM335x processor to handle the most stringent power budgets.
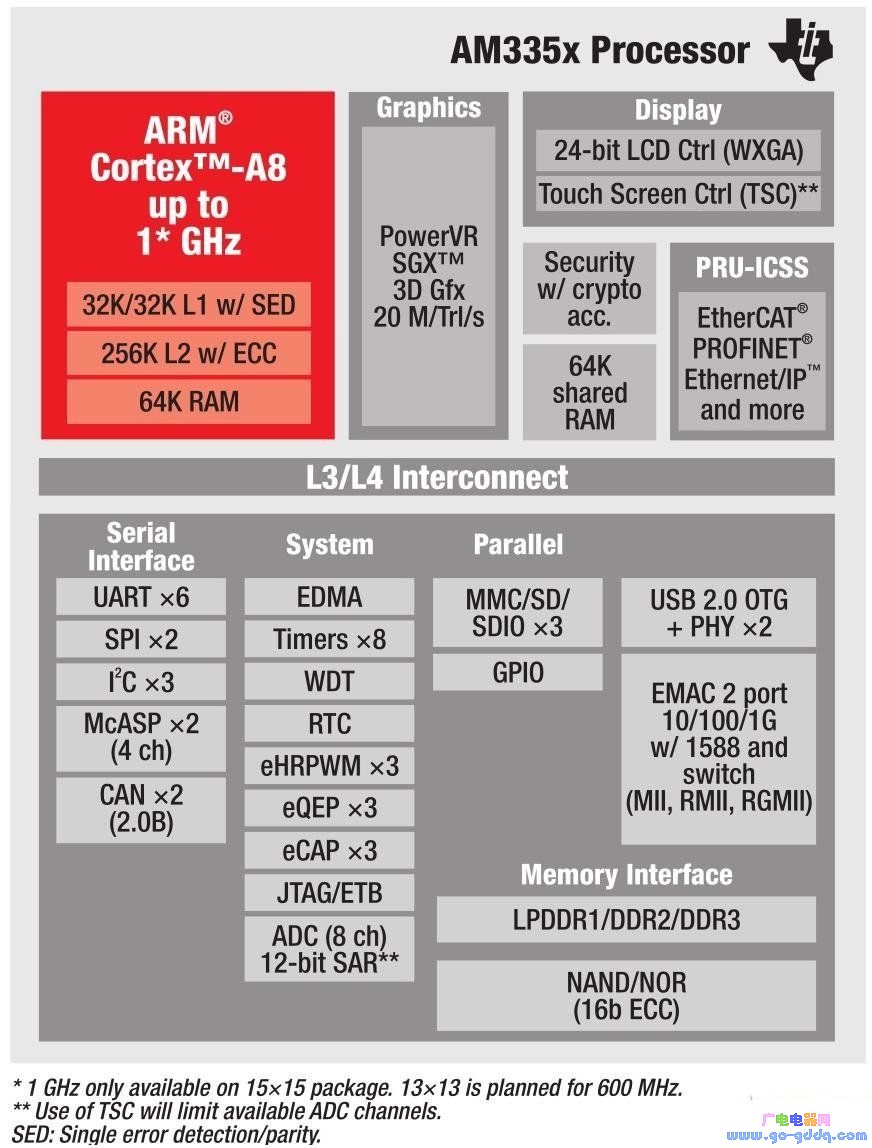
Figure 2 Sitara ARM AM335x processor structure
The AM335x solution has multi-protocol communication capabilities that eliminate the need for protocol processing for dedicated discrete ASICs or FPGAs. This essentially reduces the bill of materials cost of the slave device by 40%. The integration of support for many popular protocols (eg PROFIBUS and EtherCAT) into the AM335x processor greatly simplifies the workload of the AM335x processor-type device networking. For example, to connect an AM335x processor-type sensor to a factory automation system, it is usually only necessary to program a typical PHY or UART interface, which is very familiar to most industrial programmers. Reduced deployment time and cost by eliminating the need for hard learning.
The key to the success of the AM335x embedded processor in industrial control systems is its programmable real-time unit-based Industrial Communication Subsystem (PRU-ICSS), which enables on-chip multi-protocol processing and ensures the necessary delayed communication for master and slave devices. The PRU-ICSS consists of two 32-bit RISC processing cores running at 200MHz. It can be executed in a single loop and its direct I/O interface samples at 5 nanoseconds, ensuring the high throughput rates required for real-time communication. The PRU-ICSS is also equipped with a complete memory subsystem consisting of a core-specified shared memory and a 32-bit interrupt controller. These functions, along with their logic, control and algorithms, make PRU-ICSS an ideal choice for real-time slave communication interfaces that support all popular industrial automation protocols including PROFIBUS/PROFINET, EtherCAT and Ethernet/IP. Due to its programmable nature, PRU-ICSS can also implement custom intellectual property (IP) or custom underlying buses.

Figure 3 PRU-ICSS structure diagram
The AM335x processor is a general-purpose SoC that effectively implements most of the functions in industrial automation networks. For example, an alternative feature that supports 2D and 3D graphics is particularly suitable for HMI units. In addition, thanks to support for advanced operating systems (HLOS) such as LinuxTM, Windows® embedded CE and AndroidTM, operators can easily interact with HMI and other applications when using the AM335x SoC. Many real-time operating systems (RTOS), including TI's SYS/BIOSTM and many other third-party RTOSs, provide developers with efficient sensor and motor driver solutions that do not require memory-intensive HLOS but require low latency Real-time performance.
The reliability and longevity of components is another key criterion for industrial automation systems. In most cases, these systems are used in harsh environments, which is a huge challenge. Due to their deployment time and cost, the expected effective life cycle of a factory automation system is usually very long. The AM335x processor proves that it is a very reliable SoC. It has a wide operating temperature range and can be continuously powered up for more than 100,000 hours. TI also guarantees that the AM335x solution will last for more than 10 years.
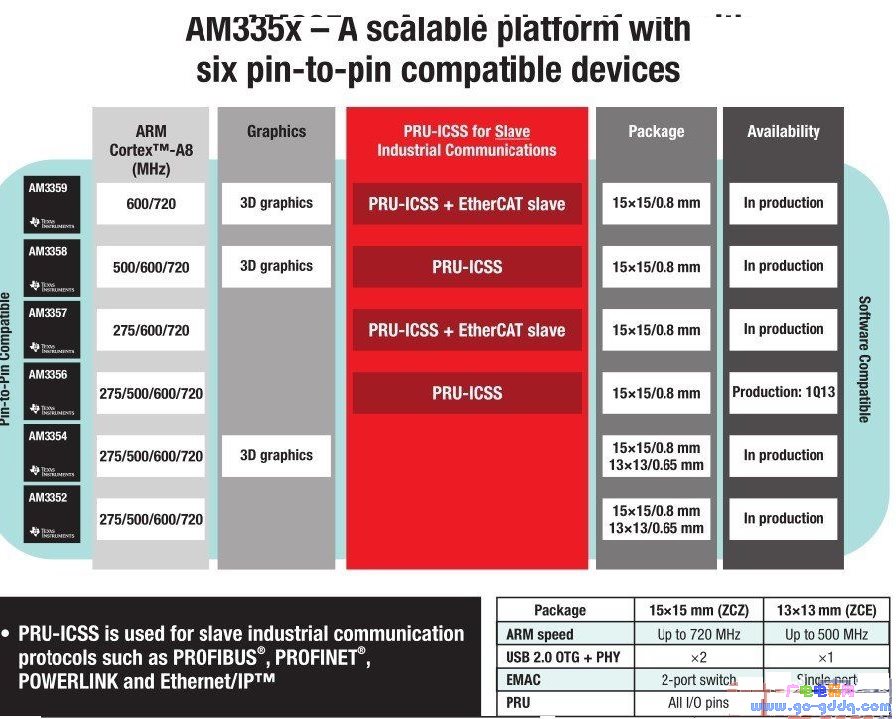
Figure 4 Sitara AM335x Scalable Platform
Seize the market opportunity
TI's factory automation solutions are supported by numerous software and hardware development tools, enabling automation vendors to quickly implement their system designs with the most advanced features on the market. In particular, the AM335x processor is supported by a simple yet powerful development tool, the Industrial Communication Engine (ICE), which gives automation vendors a cost-effective platform for developing, testing and optimizing slave communication functions. ICE provides developers with quick connections to popular industrial automation protocols such as PROFIBUS/PROFINET, Ethernet/IP, EtherCAT, and more. There are many combinations of signal LEDs for each protocol, including the three-color LEDs of Sercos 3. The eight digital outputs are connected to the onboard LEDs and the 24V output drivers. In addition, there are eight 24V digital inputs and temperature sensors for simple I/O applications. Developers can extend I/O capabilities through serial peripheral interface (SPI) communication and signals on the pulse width modulation (PWM) driver pins. Serial-based CAN and PROFIBUS fieldbus (FiELDbus) use an isolated transceiver. The module boots from external flash memory and supports serial flash, parallel flash and MMC. ICE's software environment includes TI's SYS/BIOS OS, Code Composer StudioTM integrated development environment and StarterWare (a development environment similar to that familiar to most microcontroller developers). Application kits and sample applications combined with ICE allow developers to take considerable advantage in their industrial automation applications. With the on-chip USB emulator interface, customers can start developing their own applications directly without having to purchase an external JTAG emulator.
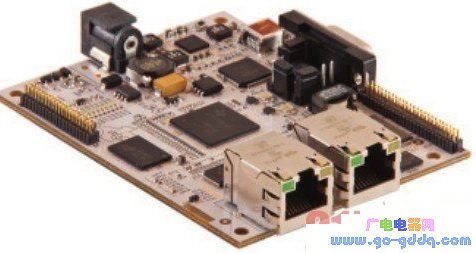
Figure 5 Sitara ICE
a highly competitive future
To meet the demands of global product manufacturing and material handling, industrial automation systems continue to increase speed, accuracy, reliability and precision. More and more manufacturers are turning to automation to increase their efficiency and reduce costs in order to achieve greater competitiveness and gain more market share. In addition, manufacturing companies strive to tightly integrate production systems with corporate business systems, including supply chain and demand monitoring systems. As a result, the communications protocol environment has become more diverse, highlighting the importance of multi-protocol support for factory automation systems and other business systems within the enterprise. The manufacturer's goal is to be a flexible, astute and highly efficient manufacturer of product materials. Leading technologies such as TI's AM335x SoC, complemented by a wide range of analog product lines and supported by numerous tools including the ICE platform, will ensure that industrial automation vendors have the capabilities they need to meet market development requirements. .
China leading manufacturers and suppliers of DC Support Capacitors,DC Capacitor, and we are specialize in Electrolytic capacitor,High Voltage Capacitor, etc.DC Support Capacitors
DC Support Capacitors,DC Capacitor,Electrolytic Capacitor,High Voltage Capacitor
YANGZHOU POSITIONING TECH CO., LTD. , https://www.cnfudatech.com